Before starting the operation of the high-viscosity pump, the casing of the gear pump is filled with the liquid to be transported, which is convenient for starting. If the ambient temperature is lower than freezing point, hot steam should be pre-introduced into the pump for pre-heat treatment before the gear pump can be started. The direction of rotation of the high-viscosity pump must match the inlet and outlet ports. If the gear pump is running for the second time, or it will be used after long-term idle, it is better to run it for about an hour under no-load or light-load conditions. If abnormal temperature rise, leakage, vibration and noise are detected in advance during the running-in phase, the machine should be shut down for inspection.
The support or flange of the high viscosity pumpS and its drive motor should use a common installation foundation. The foundation, flange or support must have sufficient rigidity to reduce the vibration and noise generated by the gear pump during operation. The motor and the gear pump must be connected by an elastic coupling, the coaxiality is less than 0.1 mm, and the inclination angle should not be greater than 1 degree. When installing the coupling, do not hit with a hammer to avoid damaging the gears and other parts of the gear pump. If driven by pulleys, sprockets, etc., brackets should be provided to prevent the driving gear bearings from being subjected to radial forces. When tightening the ground screws of the gear pump and motor, the screws should be evenly stressed and connected reliably. When turning the coupling by hand, you should feel that the gear pump can easily rotate, and there is no abnormal phenomenon such as jamming before you can pipe. A check valve is installed on the output line of the high-viscosity pump. In this way, when the pump and the output pipeline are repaired, the liquid in the system will not reverse. When the gear pump is stopped with load, it can also prevent the pump from reversing and generate a partial vacuum in its output pipeline. It should be noted that the outlet check valve cannot be reversed or stuck. The outlet pipe of the high-viscosity pump should also be provided with a protective device such as a valve, so that once the outlet channel of the pump is blocked, the valve can be opened to relieve pressure. The valve can be cast integrally with the pump body or pump cover or can be assembled separately. For high-viscosity pumps that require forward and reverse rotation, valves are required on the inlet and outlet pipes.
The pipe diameter of the suction port of the high-viscosity pump is generally large. Sometimes, the diffusion-type suction port is used to expand the volume of the low-pressure area to reduce the flow rate of the inlet liquid and reduce the suction resistance of the pump. This structure can also reduce the radial pressure acting on the journal and bearing, and extend the service life of the high viscosity pump. A check valve is installed on the output pipeline of the SS high viscosity pump, so that when the pump and output pipeline are repaired, the liquid in the system will not flow back. When the gear pump is stopped with a load, a partial vacuum is generated in its output pipe to prevent the pump from reversing. The outlet pipe of the high-viscosity pump is also provided with a protective device such as a valve, so that once the outlet channel of the pump is blocked, the valve can be opened to relieve the pressure. The valve can be cast integrally with the pump body or pump cover or can be assembled separately. In particular, it is indispensable to install check valves in places where the pressure requirements of some system equipment are strict.
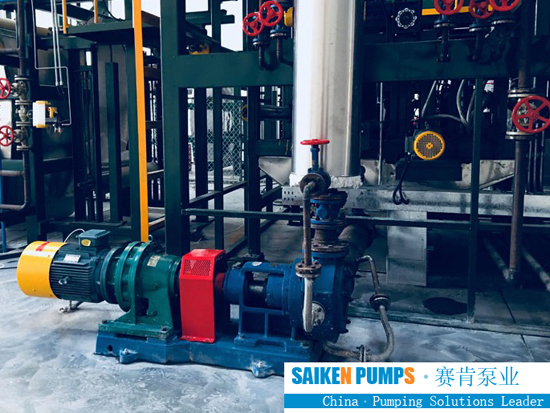
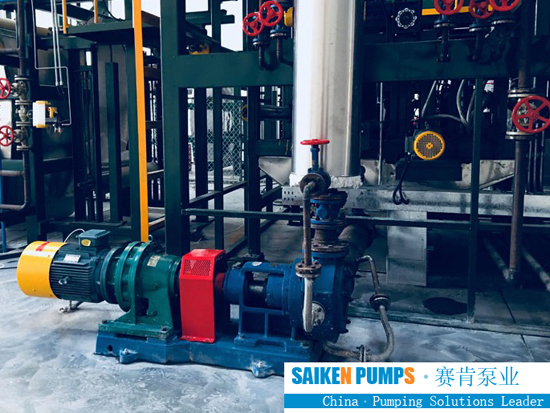