Main points of operation of diaphragm pump and process improvement
1 exhaust
1) Water injection and exhaust
The coal slurry cavity water injection exhaust has two purposes: ① Liquid end exhaust. The exhaust of the coal slurry chamber is completed by connecting the flushing water control valve on the inlet pipeline and the drain valve on the outlet pipe; ②Automatic addition of propellant. When the original oil is filled with water, the diaphragm will be forced to move to the back of the diaphragm cavity, which is the automatic filling position. In order to obtain enough hydraulic pressure to push the diaphragm to this position, the opening of the drain valve on the outlet pipeline can be controlled to complete automatic liquid filling. The most critical part of water injection and exhaust is water pressure control. The pressure provided by the pump manufacturer is 013MPa. In actual operation, it is generally controlled at 0128~0135MPa. If it is too high or too low, it will cause too much or too little oil in the propulsion cavity, and the diaphragm will be in Damaged during operation.
2) Filling and exhausting
The purpose is to fill the propellant cavity with oil. The filling process is continuous and automatic. During filling, the exhaust valve must remain open until there is no air when the propellant is discharged. At this time, the control rod has moved away from the trigger position, and the filling process will automatically stop within one minute. At this time, the propelling fluid chamber is full, but for the piston, the diaphragm has not yet reached the proper position, which will be filled by turning the car. The manufacturer recommends using manual cranking to complete the filling, but manual cranking is not only time-consuming and laborious, and it is not easy to fill the propulsion fluid chamber to the best state, so a low-load start pump is used instead of manual cranking to complete the filling of the propulsion fluid chamber. Liquid, start low load is selected as 10%.
3) Exhaust during normal operation
In the normal operation of the pump, due to the dissolved gas in the propellant, seal leakage and other reasons, the more gas in the propellant cavity will accumulate, which will damage the diaphragm. Therefore, the propellant cavity should be vented regularly.
2 buffer tank
In order to have a stable pressure and flow when the pump is working, there are buffer tanks on the inlet and outlet pipes of the pump. The buffer tank should be pre-charged with nitrogen to a certain pressure. In principle, the pre-charge pressure cannot be lower than 30% of the maximum working pressure and higher than 80% of the minimum working pressure. Although a higher pre-charge pressure can produce a better cushioning effect, when the pressure drops, it will produce pulsation, frequently impacting the bottom of the tank and causing damage to the metal internals.
When the working pressure range is large, only the pre-charge pressure is required to reach 30% to 35% of the maximum working pressure. The pre-charge pressure provided by the diaphragm pump manufacturer is: the pre-charge pressure of the imported buffer tank is to 80% to 90% of the inlet pressure. The outlet buffer tank is pre-charged to 60%-65% of the outlet pressure. In actual operation, the inlet pipe of the pump vibrates greatly, indicating that the pre-charge pressure of the imported buffer tank is not suitable. According to the actual situation, the pre-charge pressure of the imported buffer tank is reduced to 60% to 65% of the inlet pressure, and the vibration is immediately eliminated. Return to normal working condition.
During the operation of the pump, the pressure of the buffer tank will slowly drop due to leakage and other reasons. When the pressure reaches a certain pressure, the pump will appear unstable and accompanied by abnormal noise. If it runs for a long time under low pressure, the diaphragm is always large. The range fluctuation state is easy to cause the diaphragm to fatigue and reduce the service life of the diaphragm. To overcome this situation, the buffer tank must be punched during operation. Based on the experience accumulated in the commissioning process and normal production of the pump, it was decided to punch the buffer tank during the load operation, and the pressure gauge pointer was stabilized to achieve the sign of successful charging. Several tests have achieved good results, ensuring the pump Long-term safe operation.
3 Propellant control system
As shown in Figure 1, under normal operating conditions, the magnet on the control lever moves with the control lever between the triggers ZSH and ZSL, and the trigger is not triggered at this time.
If there is too little propellant in the propellant cavity, the magnet will move to the trigger ZSL, and the trigger outputs a pulse signal to the PLC control box. The PLC will output a signal to open the filling valve HV1, 2 or 3, and the propellant will enter the propellant chamber.
If there is too much propellant in the propellant chamber, the trigger ZSH will also output a pulse signal to the PLC control box. At this time, the drain valve HV5, 6 or 7 is opened, and the propellant will be discharged from the propellant chamber.
If the propellant system is faulty and the filling or discharge valve is continuously activated and opened for more than 3 minutes, the PLC will output a fault signal.
The above propellant injection and discharge are performed automatically, but the automatic injection and discharge procedure has been out of control due to triggers, internal parts, etc. during the operation of the pump. If it is necessary to repair, only stop processing, in order not to bring losses to production, After careful consideration, it was decided to use manual oil injection and discharge. Due to lack of experience, the exhaust valve on the propellant cavity was not opened when the first oil was injected, resulting in too much propellant filling and damage to the diaphragm. On the basis of summing up the failure experience, when the oil is manually filled again, the exhaust valve is opened, and the discharge stroke pressure of the propulsion chamber is stable as a sign of fullness. Several trials have been successful, providing a guarantee for safe and continuous production.
4 Start and stop load
The diaphragm pump is driven by a variable frequency motor. If the load is too large or too small, the short-term load fluctuation is large, and the long-term operation under low load, etc., all have an impact on the inverter. In order to avoid the above situations as much as possible, it is mandatory to open The parking load is controlled at about 30%, and it is set in the instrument so that the load increase and decrease must be completed within a period of time, and the maintenance of the frequency converter is effectively achieved in the process.
5 Instrument air and lubricating oil pressure
The instrument air and lubricating oil pressures are interlocked with the main motor. The fuel injection and drain valves of the propellant are air-closed valves. A certain air pressure must always be maintained. The minimum operating pressure of the two valves is not less than 0.4MPa, so the instrument The air pressure is generally maintained above 015MPa, even if the pump is stopped, the instrument air will not be stopped to avoid insufficient or excessive liquid in the propelling chamber. The air supplied to the valve is filtered and oil atomized.
When the pump is running, the lubricating oil pressure should not be lower than the pressure interlock value (0115MPa), and the pressure difference of the lubricating oil outlet filter should not be too large. The steel ball in the lubricating oil flow scope should be at the upper limit position. When adjusting this flow The adjustment range should not be too large, so as to avoid the instantaneous flow rate and the rapid pressure drop causing the interlock to trip.
Through the above process improvement and the mastery of the operation points, the pump always has a stable process environment during operation. In the past year of operation, only one trip due to electrical reasons has been achieved, achieving long-term, safe and efficient operation.
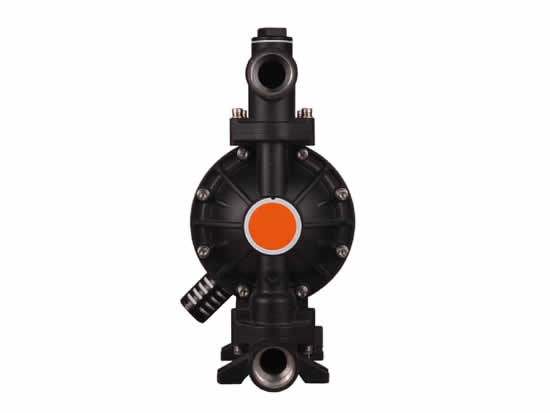
Diaphragm pump manufacturers and suppliers come from China
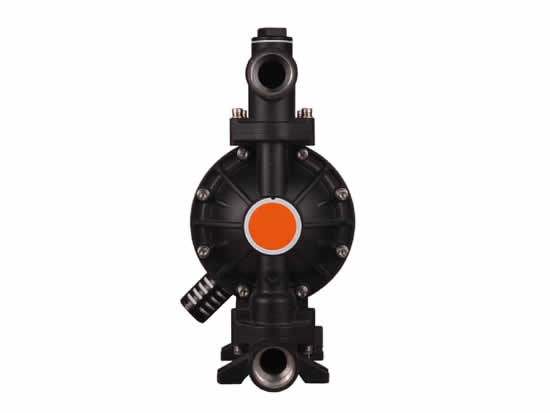
Diaphragm pump manufacturers and suppliers come from China