Distinction of Asphalt screw pump & Asphalt gear pump
The asphalt screw pump is a propulsion type positive displacement pump. The main components are the rotor and the stator. The rotor is a large lead large tooth height and a small spiral inner screw (rotor). The stator is matched with a double-headed spiral and a screw sleeve. A space for storing the medium is formed between the rotor and the stator, and when the rotor is operated in the stator, the medium is axially discharged from the suction end. Compared to gears, screw pumps deliver high viscosity materials
The concept of an asphalt gear pump is very simple, that is, its most basic form is that two identically sized gears mesh with each other in a tightly fitting housing. The interior of the housing resembles an "8" shape with two gears mounted on it. Inside, the outer diameter and sides of the gear are closely matched to the housing. The material from the extruder enters the middle of the two gears at the suction port and fills this space, moves along the housing as the teeth rotate, and finally exits when the two teeth mesh.
I. The advantages of asphalt gear pump
The structure is reliable, the work is stable, the cost is low, and the non-corrosive oil, asphalt and other viscous media can be transported; the pump itself has a safety valve, and the conveying medium has a high pressure head.


2. The shortcomings of gear asphalt pumps
It is not suitable for conveying liquids containing solid particles and liquids with high volatility and low flash point; the gears in the pump are prone to wear during long-term operation; the flow rate of the conveying medium is small.
3. The advantages of screw asphalt pump
The structure is compact, the flow and pressure are basically pulsation-free, and the pressure is higher. Compared with the gear asphalt pump, the operation is stable, the vibration and the noise are low, the service life is long, the efficiency is high, and the applicable liquid type and viscosity range are wide.
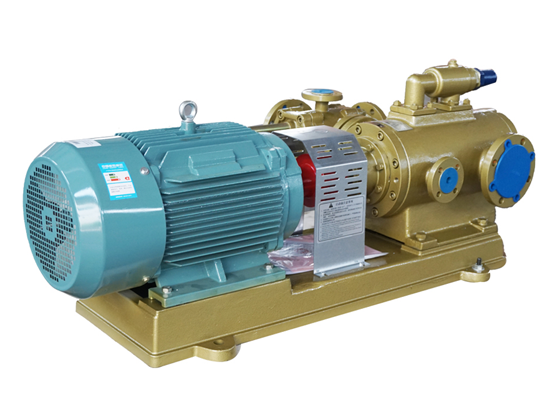
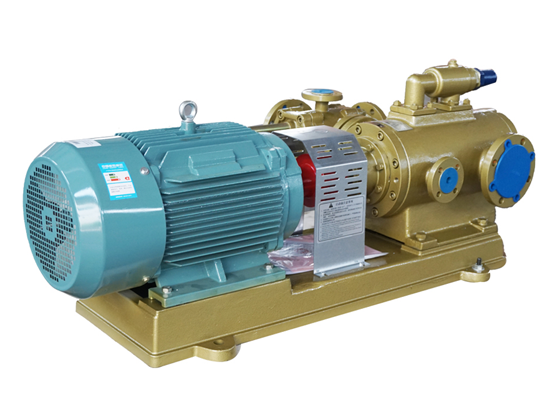
4. The disadvantages of asphalt screw pump.
High manufacturing and processing requirements, working characteristics are sensitive to viscosity changes, and the flow rate of the conveying medium is small.