The future development trend of gear pumps and gear oil pumps is high-precision, high-pressure gear pumps; high-viscosity gear pumps; high-pressure internal gear pumps, large-flow internal gear pumps; high-viscosity gear pumps, etc.
The future development trend of gear pumps and gear oil pumps is high-precision, high-pressure gear pumps; high-viscosity gear pumps, high-pressure internal gear pumps; large-flow internal gear pumps, high-viscosity gear pumps, etc. The optimized design or development direction of high-viscosity gear pumps include:
1) Develop a gear pump with double arc tooth profile as a supplement to the involute gear pump. The double-arc profile gear has less teeth, no undercutting, less wear, high efficiency, and no oil trapping.
2) Replace normal straight tooth structure with helical tooth and herringbone tooth structure. Not only can the flow and pressure pulsation be greatly reduced, but it also has a self-cleaning function. Foreign companies have even used herringbone gears in high-temperature melt pumps.
3) The use of an electric heating jacket with multiple precision sensors instead of a heat medium insulation jacket can simplify the pump operation.
4) Adopt a sun-planetary gear structure and set up multiple inlet and outlet channels to balance the radial force and reduce the occurrence of cavitation. This structure has been adopted in small spinning metering pumps.
5) Comprehensive use of spiral seals (labyrinth), mechanical seals, packing seals and other sealing structures to solve the problem of pump leakage (especially under high vacuum conditions).
6) For special occasions such as abrasive particles or strong corrosive media, consider the external bearing gear pump with two leakage points. The specially processed working gear can replace the cam rotor and the synchronous gear at the same time.
The suction and discharge principle of a gear pump is similar to that of a lobe pump. That is, the working gear is disengaged from the suction port to form a vacuum to suck up the material. As the gear rotates, the liquid in the tooth groove is brought to the discharge port and discharged under the high pressure generated when the gear enters the mesh. The old-fashioned viscosity gear pump is also very close to the lobe pump in structure. A pair of working gears are also driven by synchronous gears. There is no direct contact between the working gears. The bearing is external and has 4 leakage points. Therefore, this structure has no advantages at all.
Gear pump is also a product of oil pump series.
However, the structure of high-viscosity gear pumps has undergone revolutionary changes in recent years. The comprehensive application of a large number of new technologies, new materials and new processes with forced lubrication of materials as the primary feature of integral built-in sliding bearings has made the application range of gear pumps more and more extensive, especially in the transportation of high temperature and high pressure molten polymer. It is almost impossible to replace other positive displacement pumps. Foreign companies are represented by Viking of the United States, ROTAN of Denmark, MAAG of Switzerland, and SHIMADZU of Japan. Domestically, the Sichuan Provincial Machinery Research and Design Institute is the representative. The transmission institute of this institute gathers the strengths of many families. The high-viscosity gear pumps of external gearing and internal gearing developed by this institute have been successfully applied to vinylon, acrylic, poly Many industries such as ester chips and viscose fibers. The project has been appraised by the Sichuan Provincial Science and Technology Commission and won the third prize of Sichuan Science and Technology Progress Award.
At present, it seems that the use of multi-tooth difference internal meshing cycloidal gear pump is ideal for ordinary high-viscosity occasions at low temperature and low pressure. The driving gear is an internal gear with a claw-shaped arc curve, and the driven gear is embedded in it with a special cycloid tooth profile. The number of teeth is 11 teeth and 8 teeth respectively, and the middle is separated by a crescent plate. The pump has extremely compact structure, large flow, low noise, high efficiency, and can adapt to changes in medium viscosity in a large range.
For high-temperature and high-pressure occasions such as polyester, external meshing melt gear pumps are used. The working rotor is a pair of high-precision hard-toothed gears. The gears and shafts are integrally processed and all precision ground and polished. The whole is made of tool steel. The unloading groove is opened on the end surface of the sliding bearing, and the high-pressure material is led to the bearing mating surface for lubrication and cooling (relatively speaking), and finally returns to the suction cavity. The pump has very high accuracy, puncture, volumetric efficiency, and dimensional stability. The applicable temperature has reached 450℃, the applicable pressure has reached 30MPa, and the applicable viscosity has reached 4×10 6 cP.
According to the above, it can be seen that various types of high-viscosity pumps have their own characteristics and shortcomings, but relatively speaking, with the continuous development and continuous improvement of gear pumps, they are simple, reliable, low-consumption, and widely applicable. The trend of taking the lead in the field of high viscosity has become more and more obvious.
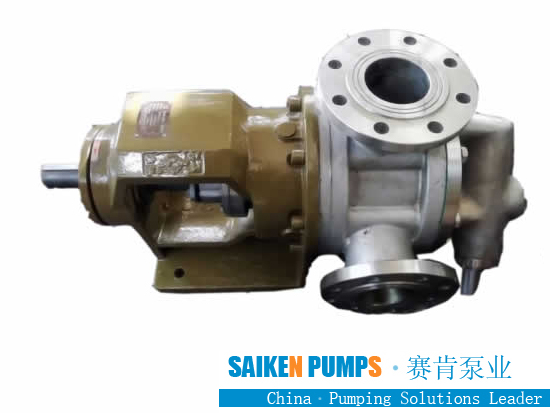
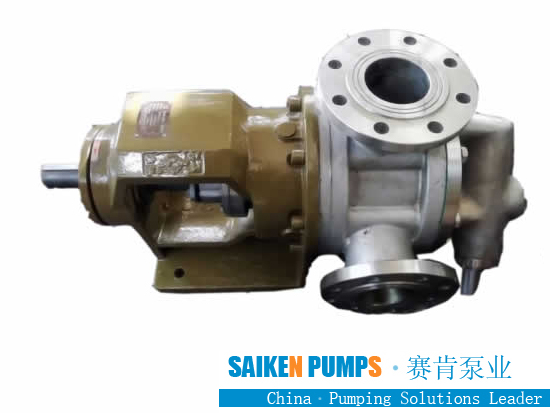